Before I get to the now commonplace, nearly expected, change of plans, here is a small piece that I needed to make for the tailcap switch unit. The switch will be recessed a little and needs an actuator rod. I made this from a piece of 3/8” dowel and a scrap of 1mm FRP. I made the FRP round using my sander jig apparatus. Then I glued the dowel into a 3/8” hole I drilled in the FRP and cemented the joint with some Kafuter UV activated adhesive.
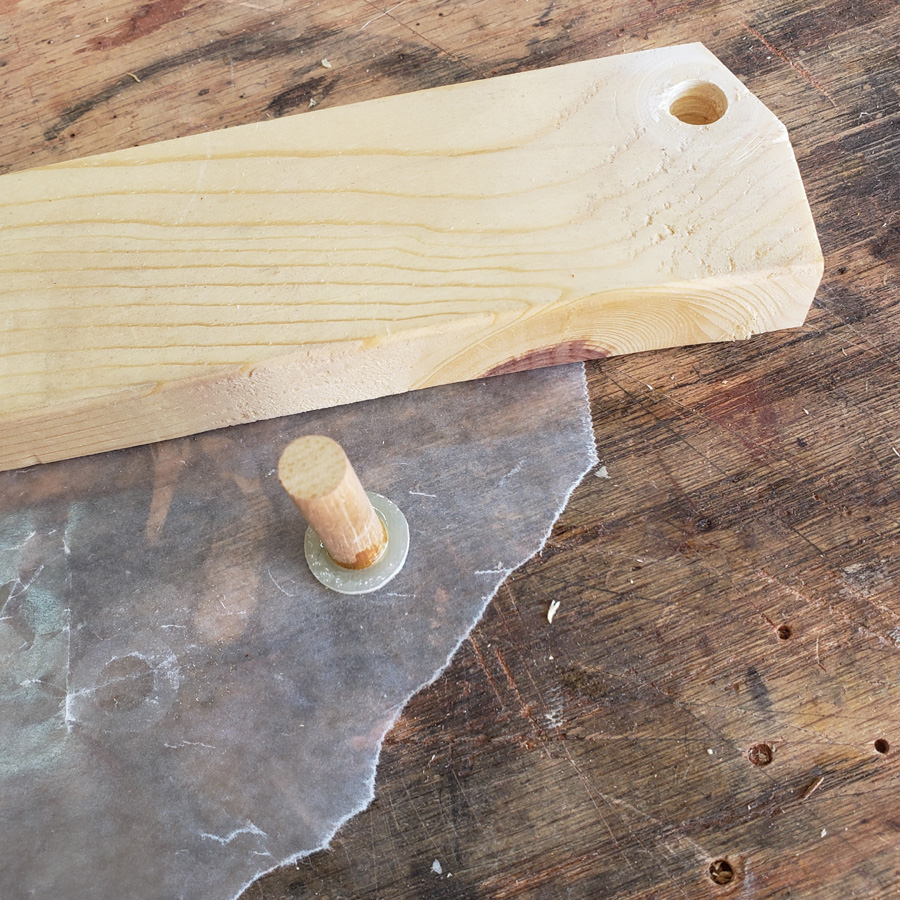
I decided to give the body a coat of clear lacquer. My reason for doing it now was to keep the wood clean as it is being handled a lot at this stage.
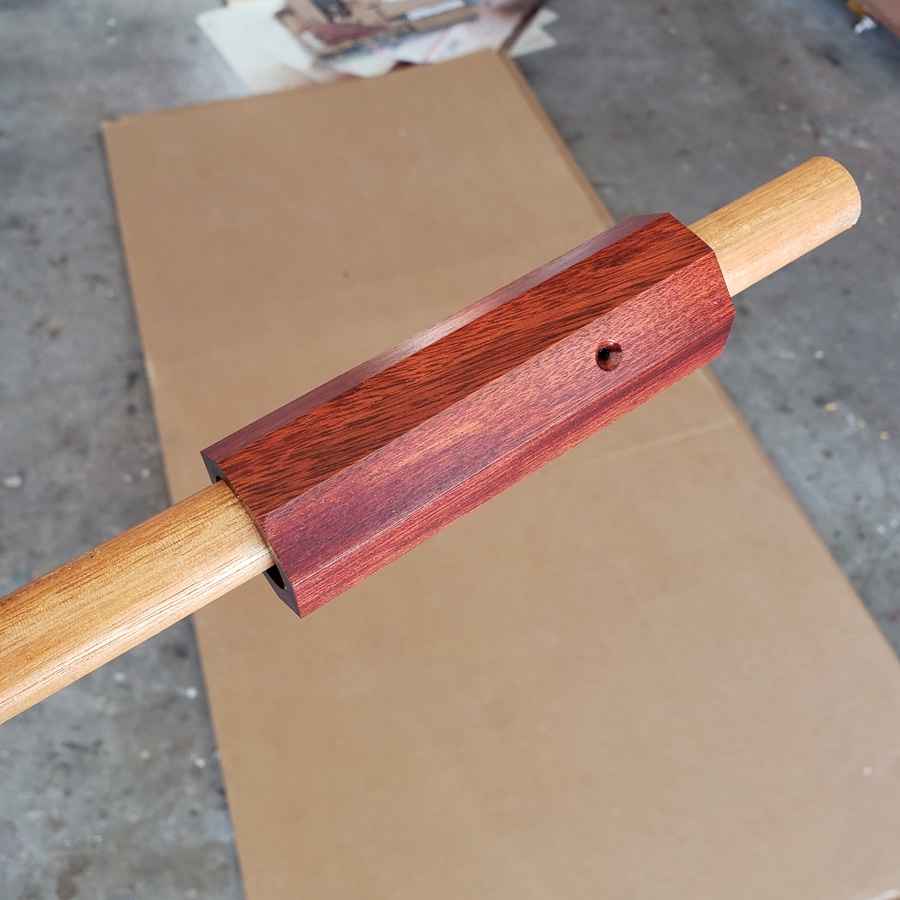
I used spray lacquer and a wood dowel to hold the body piece.
Now for another change. I forgot to take a photograph of what caused this change. Way back, when I made the head of this light I used two machine screws through the head to secure the head to the heat sink and front copper disc. I planned on using a similar system to secure the tailcap to the tail end of the wood body. I had a memory lapse. I didn’t double check
, but I thought I had used 4-40 socket head machine screws for the front. The socket heads were fitted into two drilled recesses to alllow the machine screw heads to be flush with the surrounding wood surface. Alas, I has used smaller 2-56 machine screws. The 4-40 machine screws have a larger diameter head. That head OD is large enough that the desired recess holes would cut into the perimeter, would break out of the octagon side of the tailcap.
An aside thought… this light should be thought of as a prototype I suppose. (A prototype is an early sample, model, or release of a product built to test a concept or process.)
I gave some thought to not recessing the heads, or to using flatheads instead. However the flathead countersink would run into the same problem of “not enough meat in the edge to allow it to work”. With only two screw heads protruding it would not be possible to tail stand the light. I thought of adding two more machine screws, but gave that up as protruding screws at the tailcap would conflict visually with the recessed heads of the front end.
The solution I came up with was to use 2-56 screws on the tailend. To achieve this I cut a new cap piece to glue over the 4-40 holes in the tailcap. I would drill new holes in the octagon face edge one section over.
So, here’s a new piece of bocote being glued and clamped…
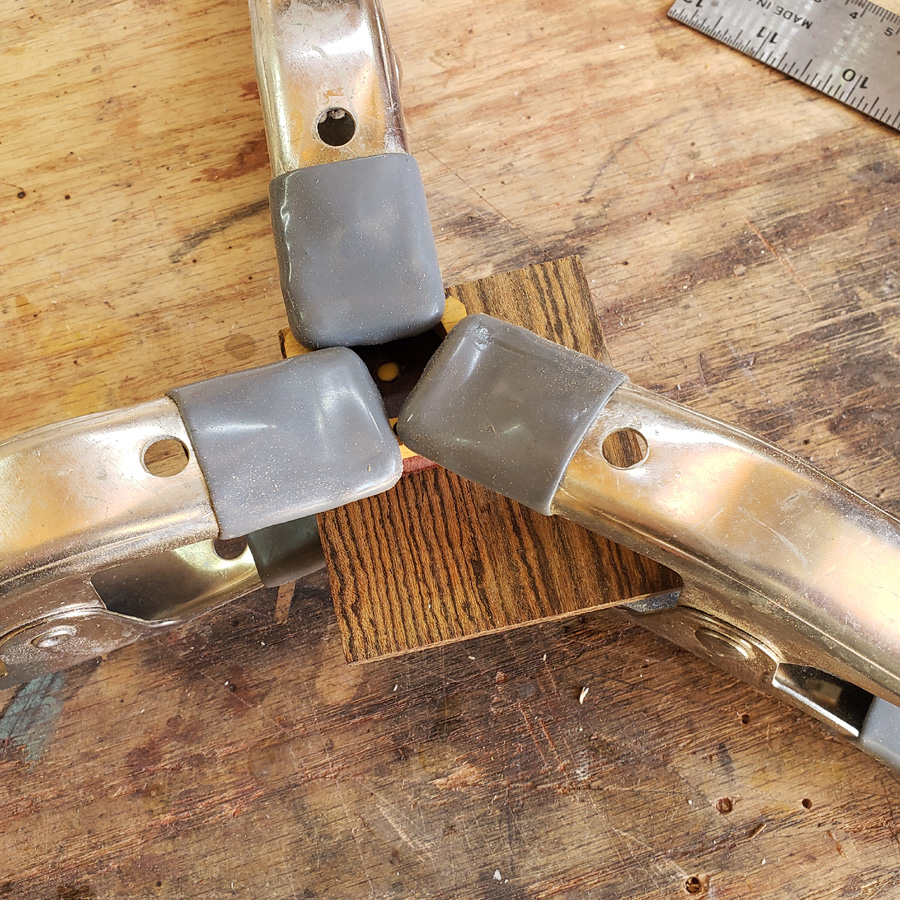
The finished cap with the bocote was sanded down to an octagon shape. I also cut down the bloodwood length before gluing the bocote cap on; no need to have such a long tailcap.
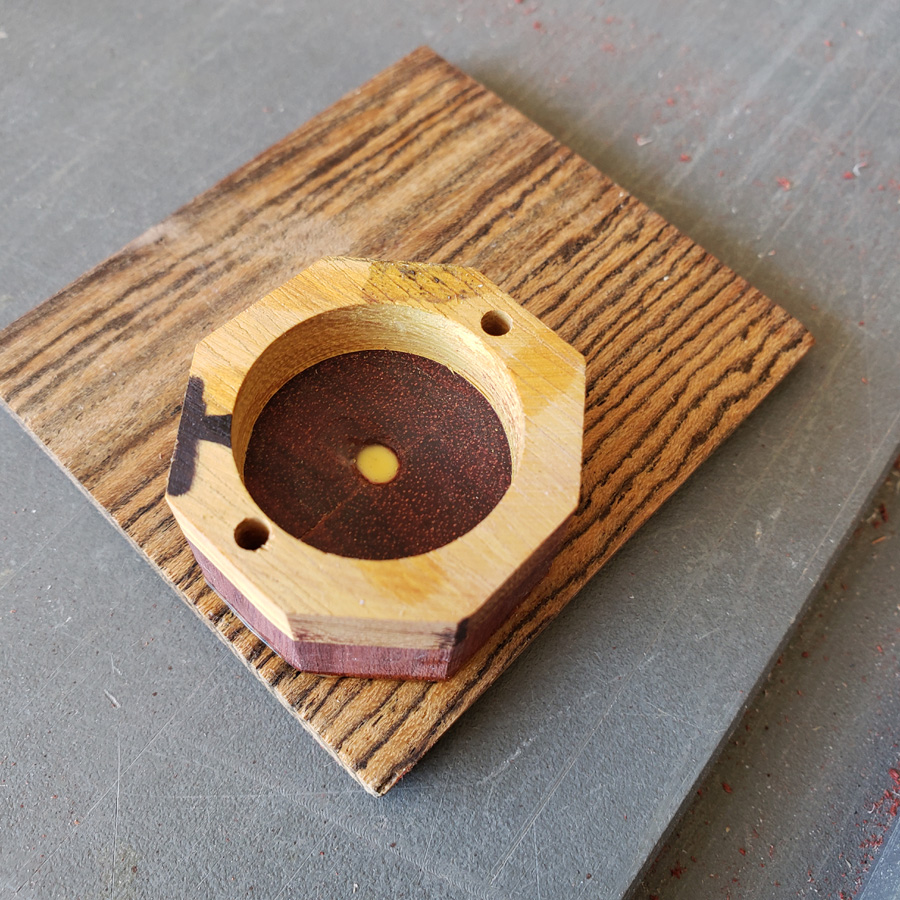
I used the two 4-40 pins to hold the tailcap in position while I drilled the first 2-56 sized hole through the tailcap and into the bloodwood body tube. I did get close enough to the epoxied in place copper tube insert that the threads actual are cut into the side of the copper as well as the bloodwood. And I had to cut a recess in the inside of the cap as the position of the hole was such that the hole wanted to drift when being drilled. Anyhow that is hidden, right! And it is a prototype.
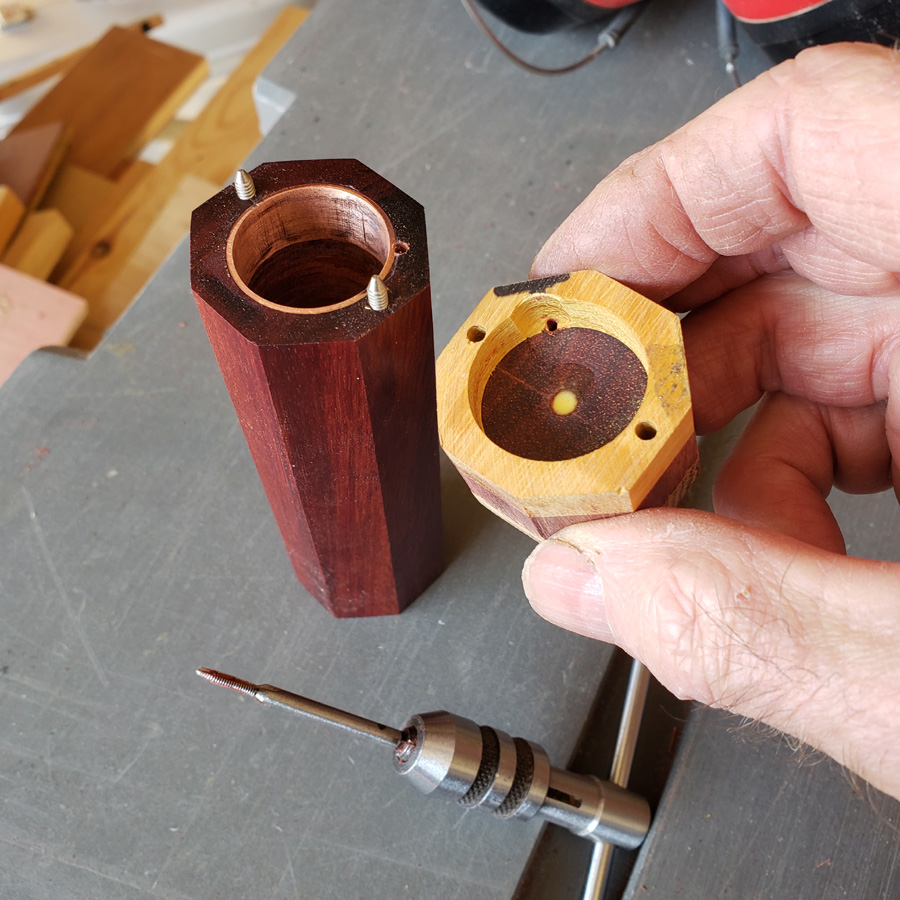
With the first 2-56 machine screw hole completed I trial fitted the tailcap. The 4-40 locator pins are visible. I did not have a long enough 2-56 machine screw on hand but I did find an old length of 2-56 threaded rod.
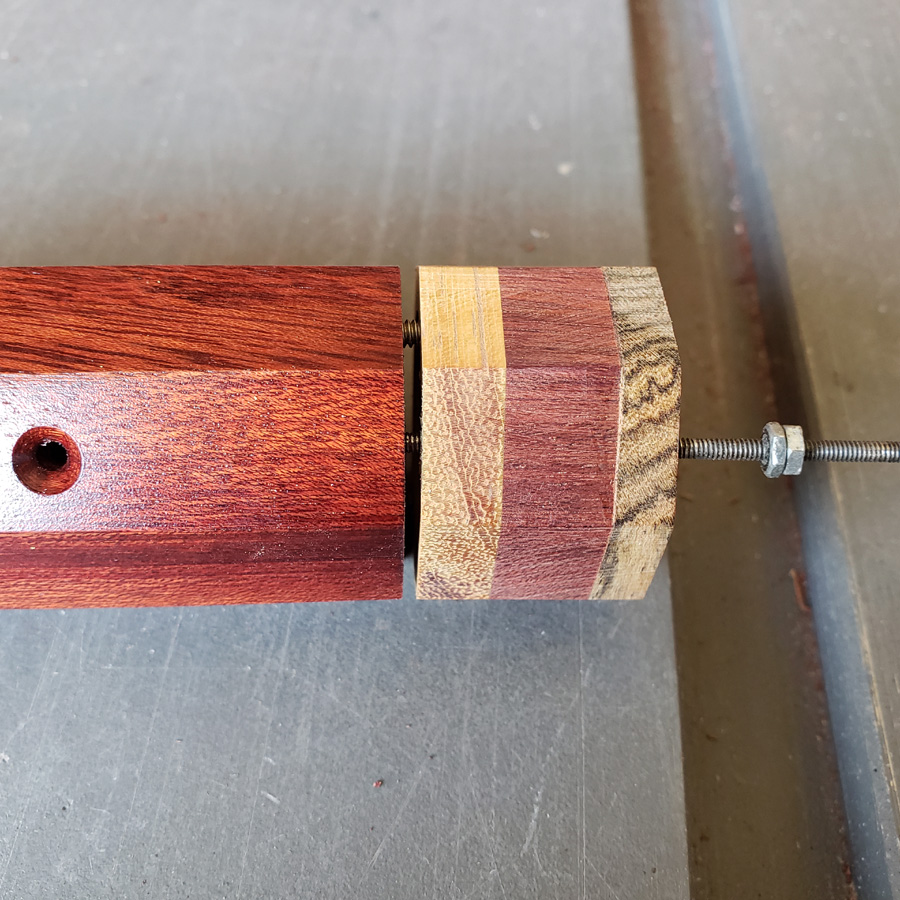
Here’s a short 2-56 socket head screw trial fitted.
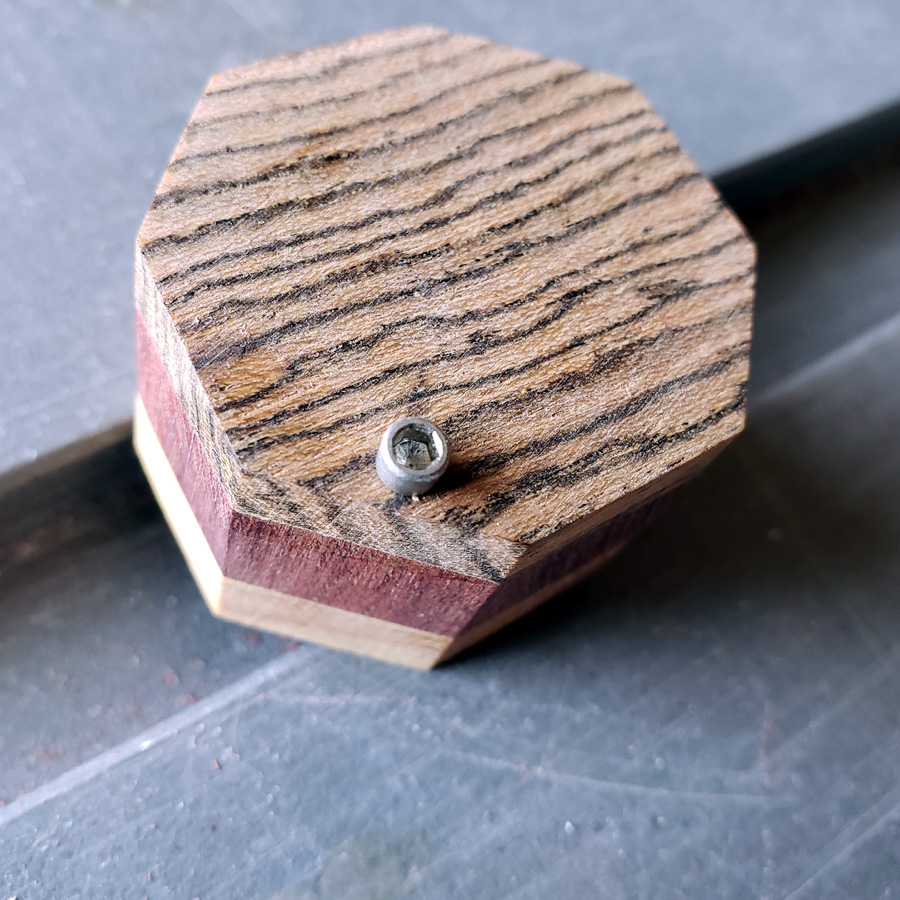
After drilling and tapping the second 2-56 hole I recess drilled and test fitted the cap to the body. The screws I had are not long enough for final use, but I have some longer ones coming. The screws pictured are only about 1/8” into the tapped holes. That is insufficient grab to last I figure.
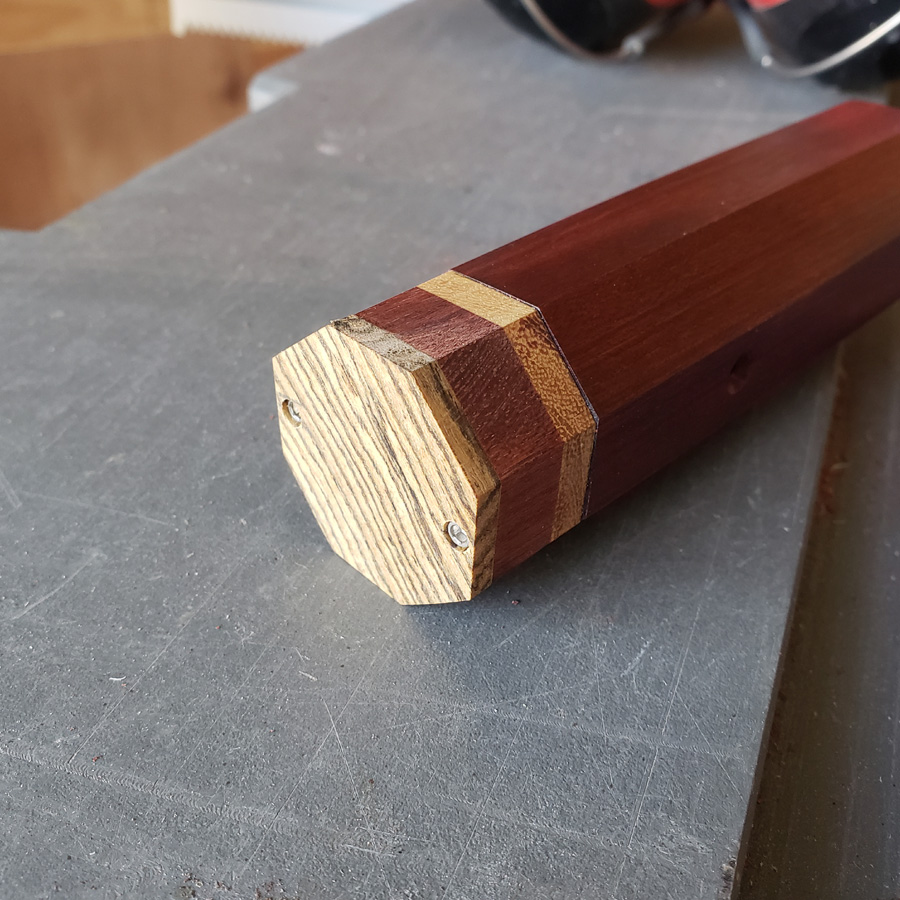
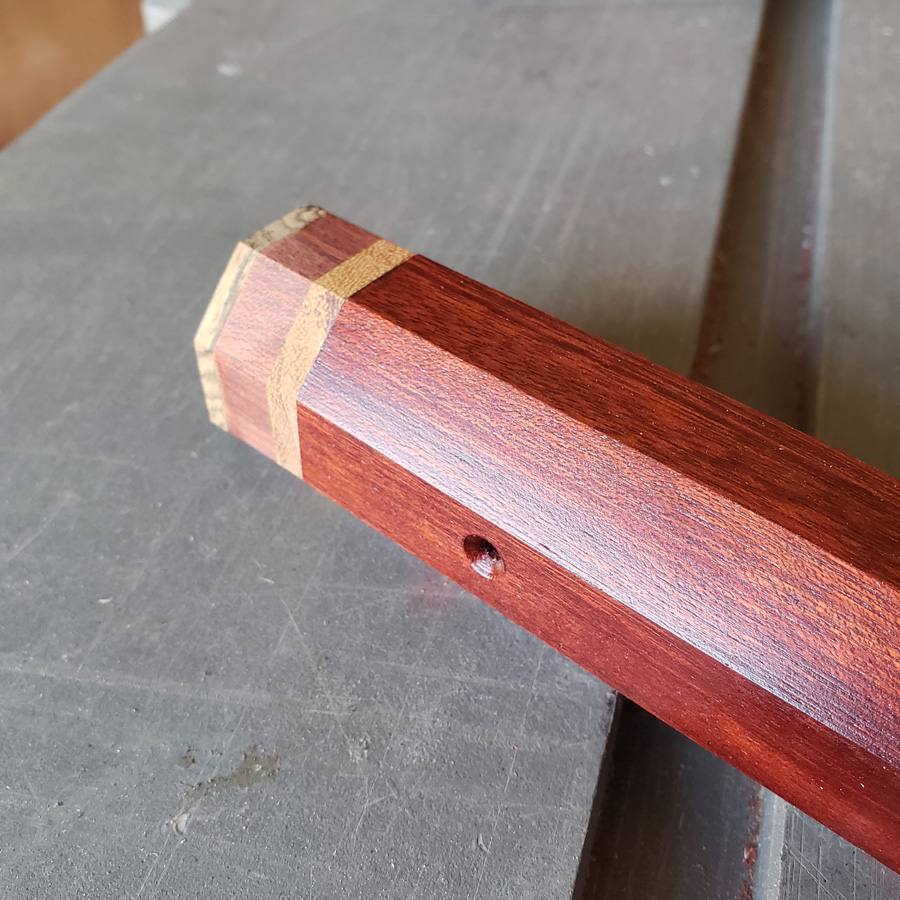
I clear coated the tailcap after removing it. Prior to clear coating I drilled the center external recess for the switch actuator rod assembly. I’m using the same diameter dowel rod to hold the tailcap for spraying as I used to make the actuator which is also displayed.
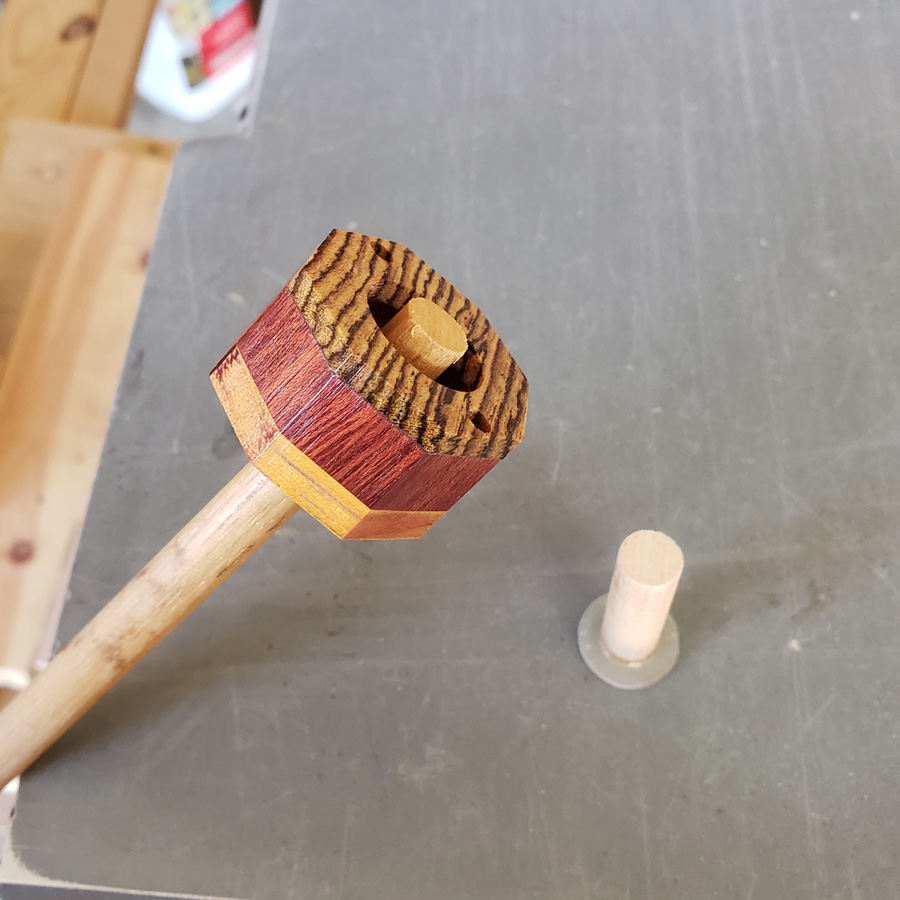
When the switch does arrive I will fit it and then trim the actuator rod and make whatever adjustments may be required.
Till later, that is all for now.
The switch is still someplace between China and here, heading in this direction, I hope.